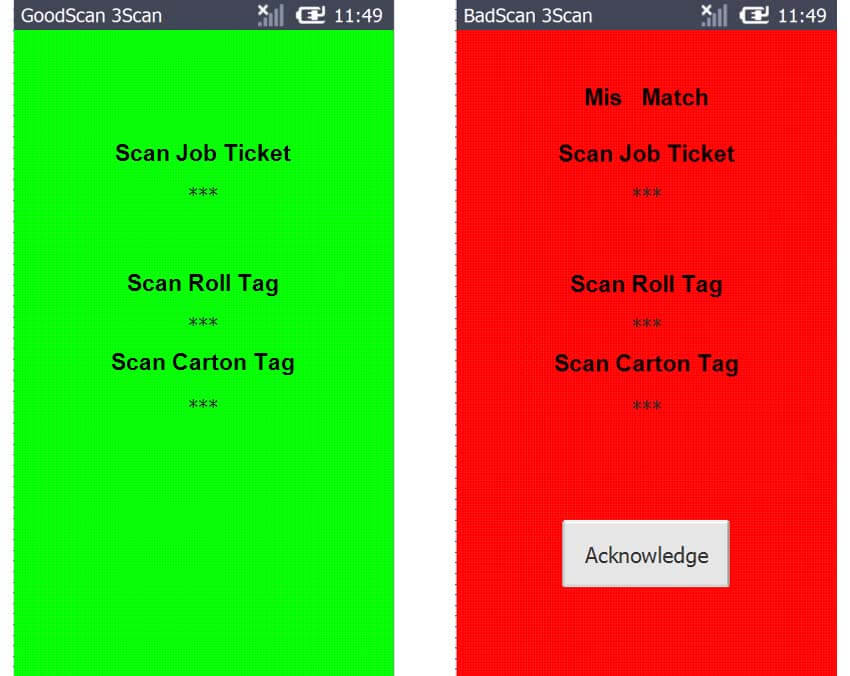
Challenge
Design a solution to minimize the shipment of incorrect labels.
Solution
Custom MCL application running on a Zebra TC52 mobile device.
Story
A large label manufacturer had many issues shipping the wrong labels to their customers. They produce consumer goods labels, and each facility has a wide variety of labels. Often there are only minute differences between various labels (i.e., the words “low fat” or “low sugar”). Unfortunately, this can cause frequent mix-ups of labels. The label manufacturer was looking for a partner to help design and implement a solution to minimize these label mix-up errors.
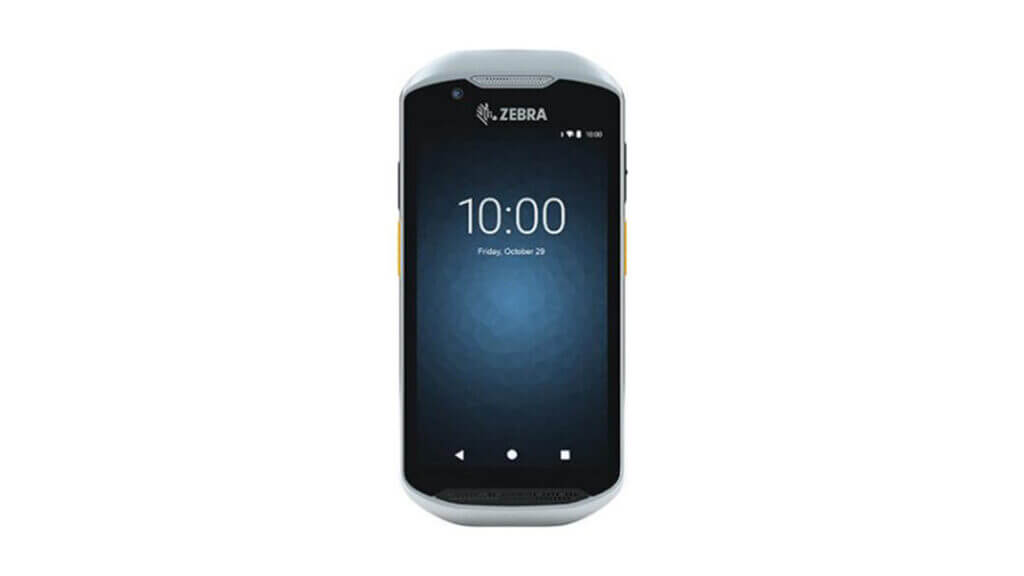
They found EMP Technical Group from online research and knew they would be excellent partners for this project. EMP began by assessing the current setup before providing a solution. After the labels are printed and slit, the rolls are placed into cartons and the cartons are loaded onto pallets. There are multiple pallets being staged all at the same time, which can also result in confusion. EMP noticed that every pallet does have a job ticket that contains the barcodes for everything that is expected on the pallet.
The engineers at EMP decided to design a custom matchcode application, using MCL, that would run on a Zebra TC52 mobile device. EMP has implemented the matchcode application many times and knew this was the best solution. The matchcode application allows an operator to scan the barcode on the job ticket and then scans the matching barcode on the core tag (inside of label roll), roll tag (outside of label roll), and the carton tag. Each of these barcodes must match before the operator is allowed to place the roll into the carton. If the barcodes all match, the application flashes green. If they do not match, the application flashes red and the operator must manually inspect the labels to find the correct ones.
Each of the matchcode scans is recorded into an Excel file. This allows the label manufacturer to refer to their data in case of a misshipment. This solution has greatly minimized the shipment of incorrect labels, and the customer is looking to implement this solution at various other locations.
Are you having trouble with mis-shipments and need a solution? Contact the team at EMP today!