Problem
A specialized parts manufacturer was looking to track parts and record calibration, or wrench torque. throughout assembly. They wanted to be able to go back and trace the origin of any problem so they could adjust their process as the prototype designs evolved.
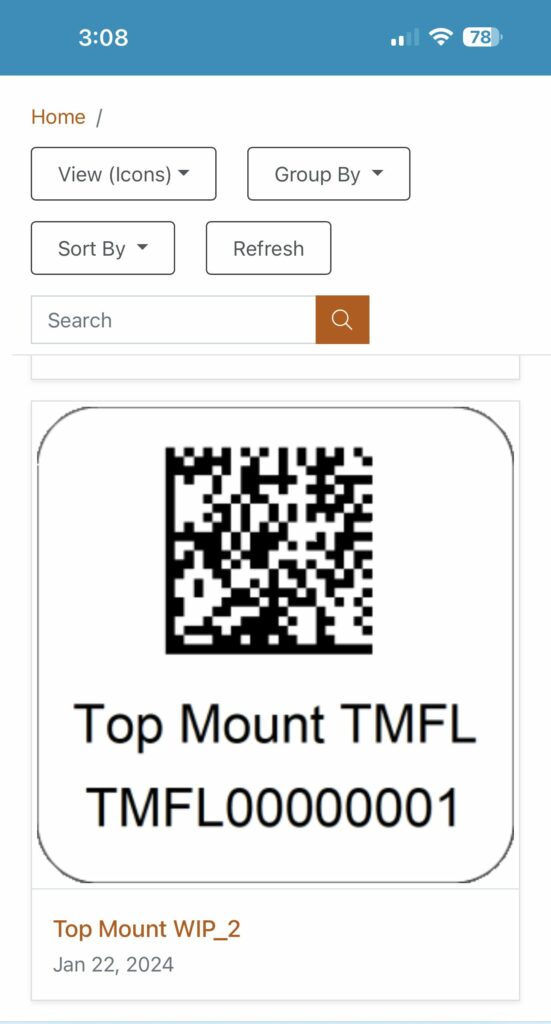
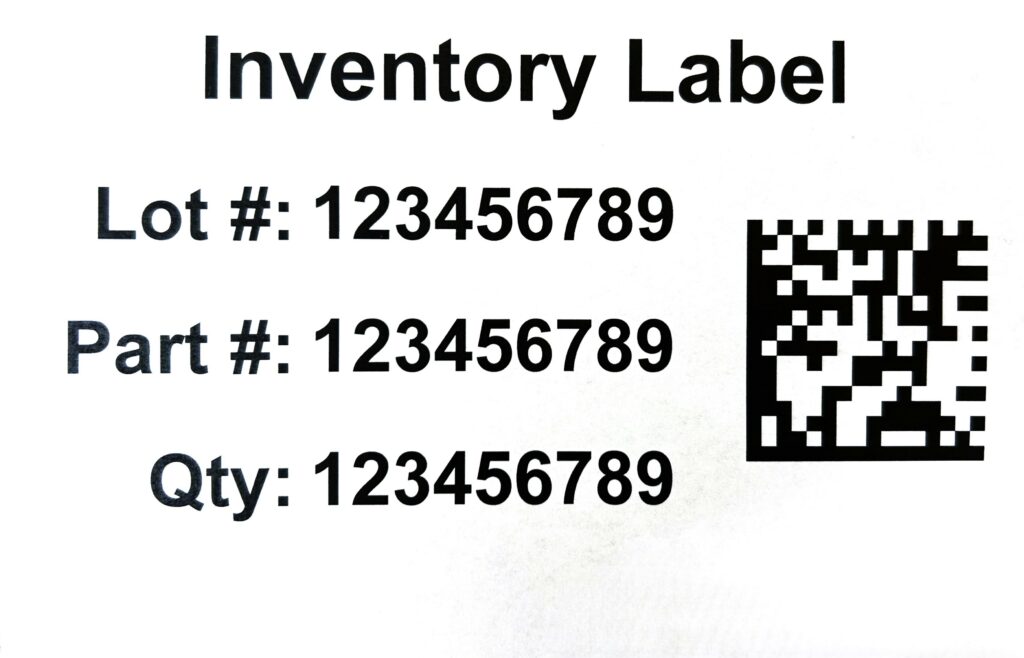
Solution
A two part solution.
Phase 1: Design and build an integrator software program that can pass along MES data to Seagull Scientific’s BarTender in order to track various stages of the prototype assembly.
Phase 2: While integration programming is being built, implement a short-term labeling system solution using BarTender, Zebra ZT411’s, and TC73’s allowing for a more complex version of Scan and Print.
Story
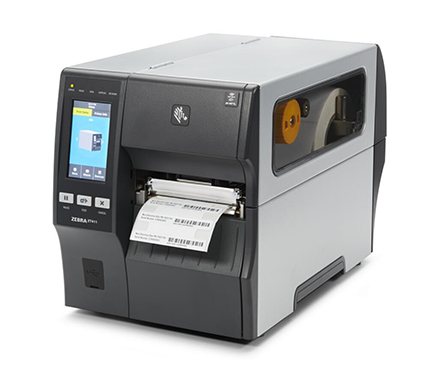
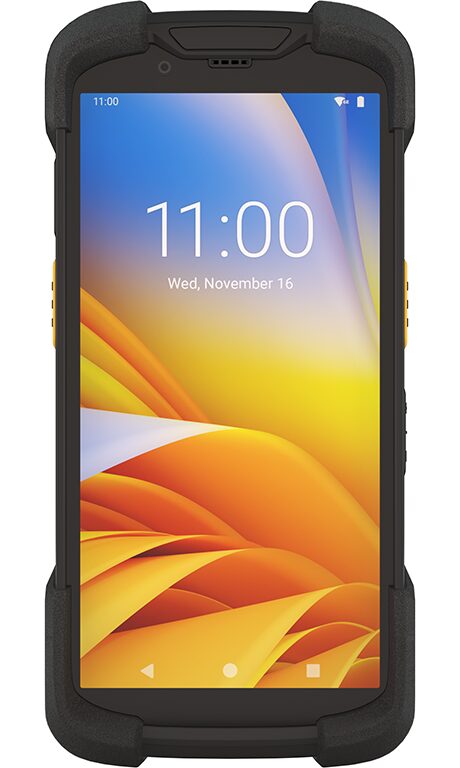
A company built an entire manufacturing site to design and test out prototype machine parts. The final parts themselves include multiple sub-assemblies made of even smaller parts. There were even calibrations and wrench torques occurring between these sub-assemblies. With such a complex assembly process involving multiple pieces, it was becoming apparent that they would not be able to backflush properly or identify the origin of a problem if there was a mistake. The ultimate solution was for EMP Programmers to build an MES integration program that would collect and send product information to BarTender in order to print labels for identification. While this was being built, EMP Engineers came up with a short term solution. This would involve the assembly operator to toggle through BarTender’s Print Portal on a Zebra TC73, choosing the label they desired, and then printing that label on a Zebra ZT411 to then apply to the part being assembled. For now, the customer can identify any origin of mistake, track parts, and backflush inventory throughout the assembly process ensuring maximum productivity and accountability.