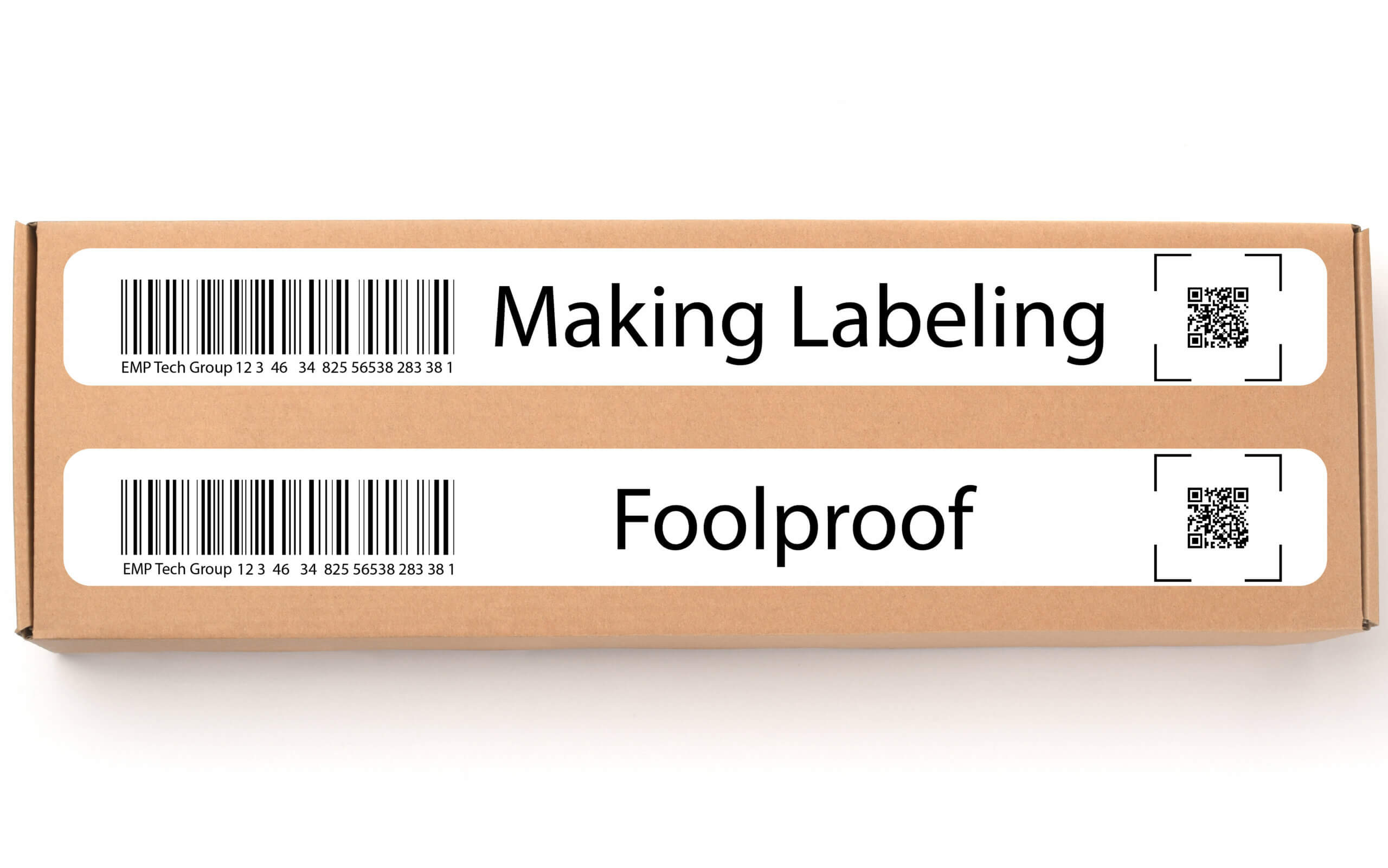
Challenge
A company was running into issues in their labeling process before shipping out various types of products. They were losing track of assigning the correct labels to product even with a two-step verification process already in place.
Solution
Error-proof the customer’s packaging workflow by writing a program that coordinates with Bartender to account for and resolve multiple types of label failure modes. This new system ensures every label is accounted for on each package.
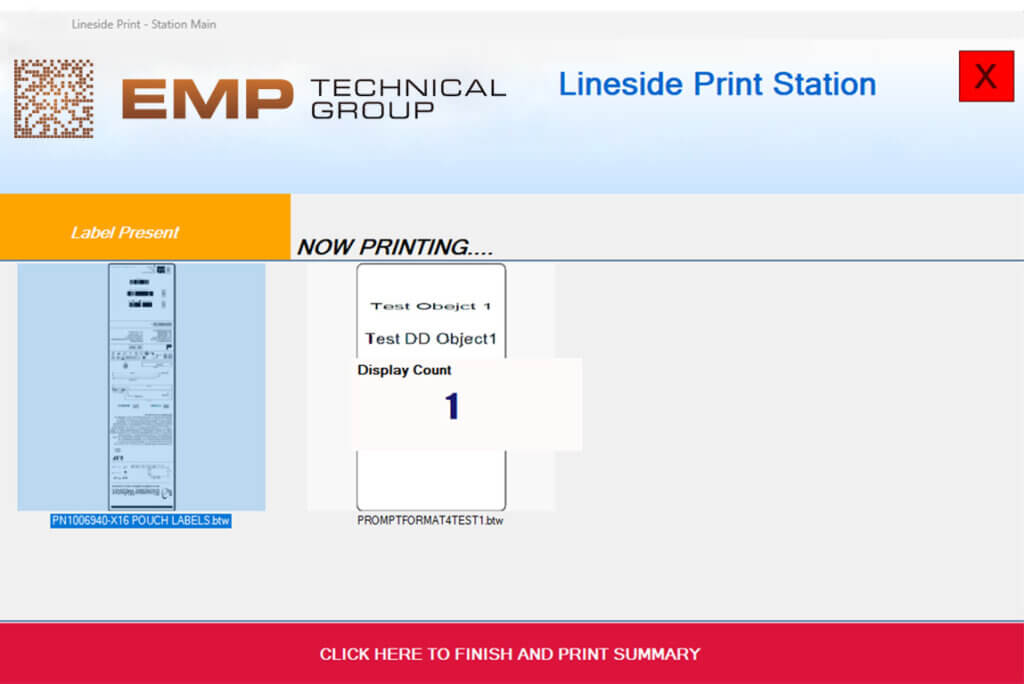
Story
A medical equipment manufacturer was running into issues with labeling their products. In facilities such as these, the printing of labels was happening in a separate room from the “clean room” where actual labels were being applied. The problem was the labels they were printing were 20″ long, leaving room for error when applying them to the boxes, requiring the need for printing extra. This caused a surplus of labels to be left lying around in the labeling room, so when a different product came in to be labeled, old labels and new labels were mixed together causing a mismanagement of inventory for their buyers. The engineers from EMP assessed over a dozen possible scenarios where the number of labels to packages could be different to ensure that no matter what, there would be one label for every package. No more, no less. After all the labels are applied and verified, the operator is then prompted to print an additional label to attach to their “job sheet” before the entire order is moved to shipping.
If you’re facing challenges with your labeling process, please reach out to the sales team at EMP Tech Group!
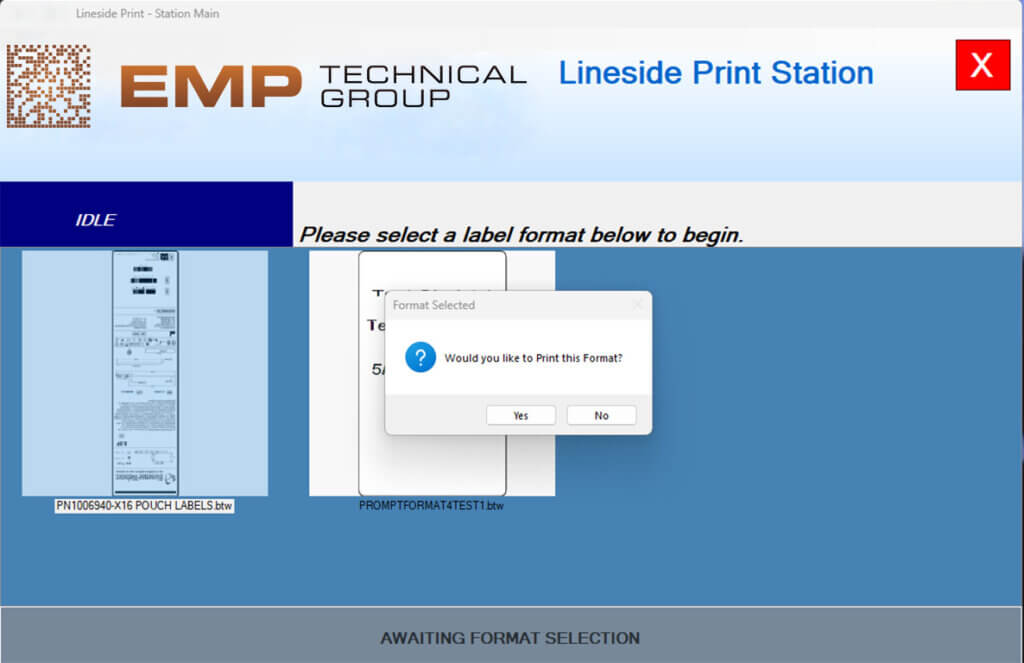