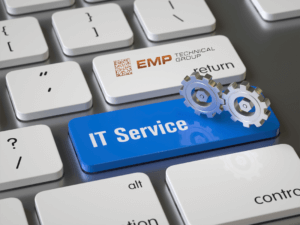
Our customers all have one thing in common: limited internal IT capacity. But from there, they split into two groups. Those who readily recognize this and are willing, even eager, to let others pitch in. Or those who still want to try to do most or all the work themselves.
There is no wrong answer to this, but some aspects of technology are specialized and tend to have a steeper learning curve. Auto ID technology and the software tools involved trend towards this more challenging end of the spectrum.
It is always a good day when a customer’s outsourced IT group brings EMP into the meeting and states that our products are outside their scope. Their expertise is in setting up servers, workstations, and networks. Handheld computers, label printers, and even wireless networking for the warehouse are things that EMP knows well. The best news is that it is a win/win. We have the expertise and repetition, which means we can do these projects quickly and efficiently. Not only saving you time but saving you money.
A couple of real-life examples.
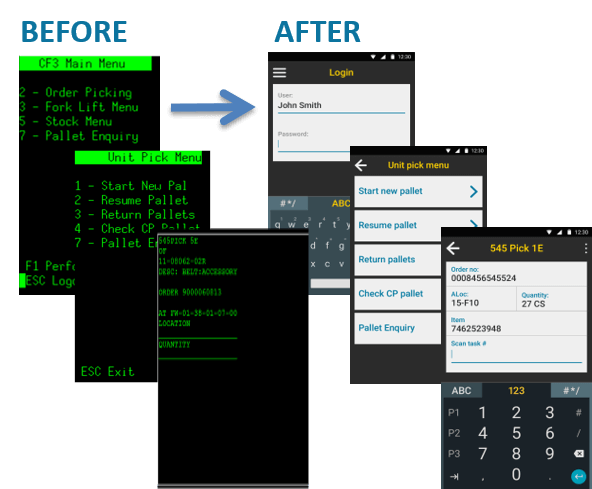
One of our customers is still running terminal emulation (actually, many are). We discussed using Ivanti’s Velocity and its screen modernization to allow them to create better screens for their application. That discussion was about a year ago, and the customer decided to investigate doing this themselves. Flash forward a year. Because of other priorities and the need to learn Velocity, nothing happened. EMP is getting ready to engage in this project and push it forward.
Second, we were recommended a few years ago to a new customer by their ERP provider for the warehouse hardware. EMP went onsite, installed the wireless in their warehouse, all the mobile computing and label printing hardware, configured everything, and trained the operators. A few years later, the customer has gone to a new ERP. The new ERP provider insisted on selling them additional hardware with no onsite configuration or training. The customer sat on the new hardware for several months, unable to get it to work. They finally called in EMP, and we had them up and running within one day, all done virtually.
Come see how we can make your automation and modernization a win/win. As always, contact us with any questions!